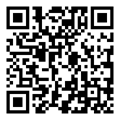
February・Company Registration and Login
June・Production equipment included
August・Forming production began.
March・ISO9002 (SGS) certification was obtained.
April・Camera Body Unit assembly began.
April・Shutter assembly began.
May・The construction of the gold mold factory and painting factory began.
August・Production of gold mold factory and painting factory began.
October・ISO9001-2000 certification was obtained.
December・Canon Company obtained SQM quality system certification.
October・The production of the cover plate unit for the exterior parts of the film machine began.
February・The construction of the new factory began.
March・The company name changed (from Grandtai Plastic to Grandtai Optical Tech).
July・New factory operation began.
November・ Stamping production began.
April・ISO 14001-2004 certification was obtained.
September・FPC assembly production began.
April・Ultra thin component forming (aperture blades)
March・Coil winding started.
March・Magnet embedding and forming (neodymium, iron, boron, and sintering)
April・Lens aperture control mold assembly
May・Two color forming began.
December・Thin feather root forming began.
Create a green environment, comply with laws and regulations, raise environmental awareness, achieve pollution prevention, promote energy saving and consumption reduction, and attain continuous improvement.
Quality first, customer foremost, with quality first as the central idea, involving all employees in production and operation activities to provide customers with satisfactory products and make continuous improvement.
Comply with legal regulations, engage in corporate activities, respect local customs and harmony, fulfill corporate responsibilities, manufacture top-notch products that meet customer and market demands with leading technology and management, innovate continuously, make improvements day by day, respond to changes in the era, and establish the foundation for the sustainable development of the enterprise, creating common prosperity together.
Injection molding: single injection/double injection
Material: IR PC+PC
Mold Technology: hot runner, gate cut in mold.
Surface treatment: glossy polish SPI-A1, logo in matte silver printing.
Advantages: no welding line on surface hole, less runners (gold runner 20g~30g→hot runner 0g~3g).
Application: IR cover, front cover.
Injection molding: double injection
Material: PC+TPE
Mold technology: forming thread by twisting mold
Surface treatment: texture
Advantages: compared to mechanical mold, precision twisting mold makes ejection of 2mm thread of product done more efficiently with highly quality.
Application: inner thread structure products.
Injection molding: double injection
Material : PC+TPE
Mold technology: special texture design with gap.
Surface treatment: 190um texture depth in large area
Advantages: meeting the requirements of cosmetic multi–level texture and light product.
Application: cosmetic products, handheld devices.
Injection molding: insert molding
Material: ①PC+LSR②(PC+LSR)+PC
Mold technology: LSR insert molding
Surface treatment: texture
Advantages: meeting the requirements of waterproof function and covering tightly.
Application: waterproof products, fixed/anti-slip products.
The product is processed through painting and printing processes, and a protective or decorative layer is applied to the surface of the product by applying specific coatings. Then print the pattern or text on the surface of the product through the concave convex changes of the printing plate.
1. Two Spindle automatic coating lines and four manual coating rooms can meet various production capacities.
2. Various reliability testing instruments are complete, and high temperature, high humidity, and surface strength are guaranteed according to customer requirements for quality assurance.
Mold forming is an important industrial production technology used to produce molded products, widely used in the compression molding or injection molding of plastics, rubber, ceramics and other products. Mold forming technology mainly includes various types such as injection molding, extrusion molding, and compression molding, each with its specific application scenarios and product characteristics.
■ Material: SUS/CU+NI+AU
■ Process: Material→Electroplating NI→Electroplating AU partially→Stamping
■ Advantages: changing the process in the past to lower electroplating cost and deter deformation.
■ Application: FPC contact brush.
■ Material: Aluminum
■ Process: Material→Bending→Blanking
■ Advantages: less process (< 10 processes) with progressive stamping, highly precision mold for bending, strokes per minute 80, 50% less than the cost of die-casting.
■ Application: heat dissipation for mini 3C products.
■ Material: Aluminum
■ Process: Material→Bending→Blanking
■ Advantages: with progressive die and precision bending technology, hole alignment through bending process many times.
■ Application: battery box gnd holder.
■ Material: SUS
■ Process: Material→Bending→Blanking
■ Advantages: bending angle of 36mm height will be less than 0.2 degree after the material is bent many times.
■ Application: main chassis (holder).
Process: melting, welding, dispensing, riveting, CNC, laser marking, assembling, inspecting, packing.
Advantages: with one stop assembling including self-production and self-purchase, we can lower the cost of packing and shipment, and shorten delivery.
Application: the assembly of products, such as camera, smart phone, automobile, security control, and smart home.
Painting Technology
Process: special cosmetic painting.
Painting: metal/plastic soft touch paint, sprinkling paint, leather paint, glossy design.
Advantages: meeting customers’special cosmetic process requirement.
Application: all cosmetic products.